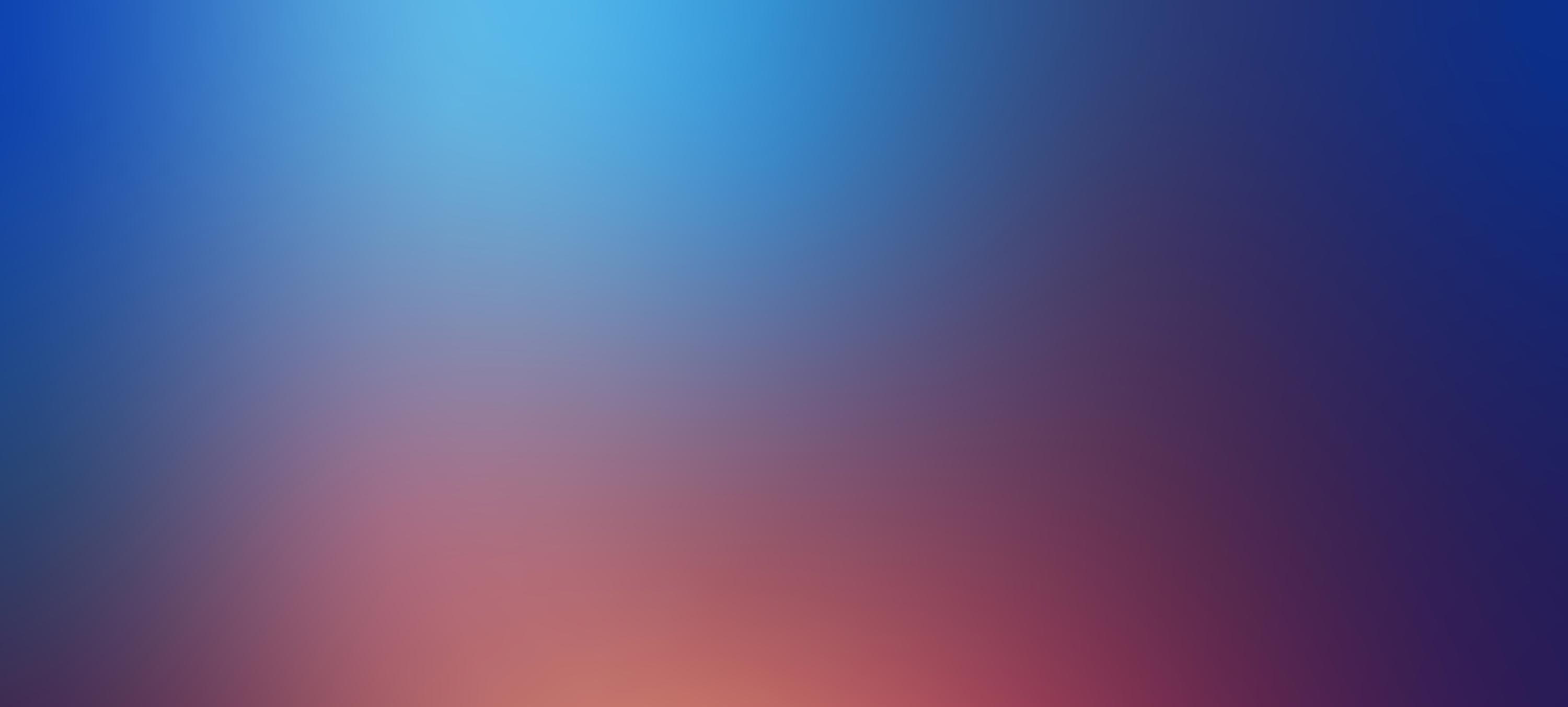
Femap with NX Nastran: Analyzing a Bracket Assembly
The bracket assembly video series introduces Femap with NX Nastran by demonstrating an entire assembly analysis cycle.
Beginning with CAD geometry, Femap is used to simplify, prepare, and mesh the geometry using an array of powerful geometry and meshing tools. Connections are created between assembly components using the Femap API and Nastran Glue. After load and constraints are applied, results are viewed in a variety of ways using the Femap Post-Processing Toolbox. Novice to experienced Femap users will benefit from the detailed discussion in the bracket assembly video series.
Bracket Assembly Analysis Part 1
Part 1: In the first video in the series, CAD geometry is simplified and prepared for meshing using Femap’s extensive geometry manipulation tools. Feature removal, midsurface creation, and surface splitting tools in Femap help build a representative mesh for an assembly.
Bracket Assembly Analysis Part 2
Part 2: Materials and properties are created for the solid, shell, and beam meshes in the assembly. Components are then meshed with solid or shell elements and manipulated with Femap’s Meshing Toolbox. The Femap API is also used to create a bolted connection.
Bracket Assembly Analysis Part 3
Part 3: Loads and constraints are applied to the assembly using a variety of Femap’s selection tools.
Bracket Assembly Analysis Part 4
Part 4: A connection is created between dissimilar meshes on components using NX Nastran’s glue functionality, and Femap’s Connection tools are used to easily build contact regions in the mesh by selecting CAD surfaces.
Bracket Assembly Analysis Part 5
Part 5: In the final video in the series, the assembly analysis is run using NX Nastran and uses Femap’s Post-Processing Toolbox to visualize results.