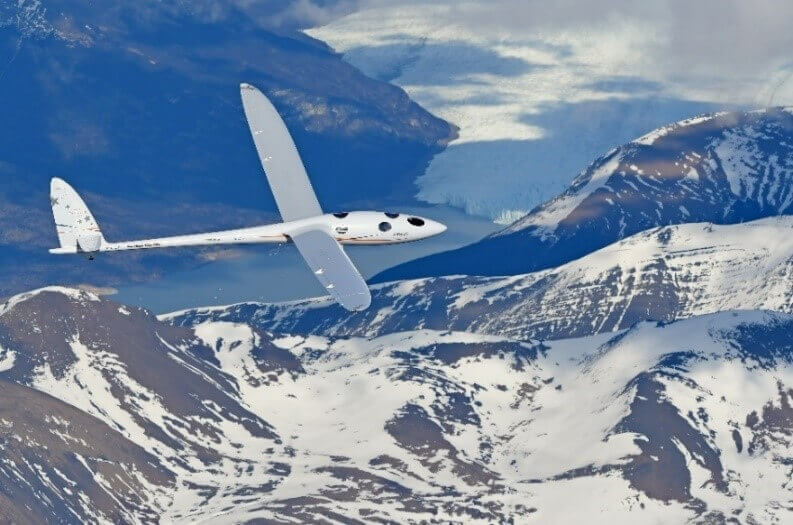
Taking A Glider from Design to Flight
Understand how leveraging Siemens solutions can enable aerospace companies to cost-effectively mature their designs and bring concepts to life with more confidence.
The history of aviation is filled with notable successes and equally catastrophic failures. One of these catastrophic failure modes is due to flutter, a dynamic instability caused by interactions between aerodynamic loads, stiffness, and inertial forces on the aircraft. Flutter typically occurs at some combination of flight speed and altitude at which the structure undergoes a positive feedback energy cycle. Because of the speed and severity of the failure caused by the flutter phenomena, the simulation and flight testing needed to safely approve the operating flight envelope is of critical importance.
In this webinar, we will explore Perlan II, a glider designed to break the record altitude for powerless flight. The Perlan Project team was very concerned about flutter due to both the high aspect ratio of the glider as well as the high altitude at which the glider was designed to operate. ATA Engineering was contracted to assist the Perlan team in taking their design from a basic solid model all the way through flight testing, where the operating flight envelope was successfully expanded. The full suite of Siemens solutions allows aerospace companies to successfully meet their performance and safety requirements all while managing project cost and schedule.
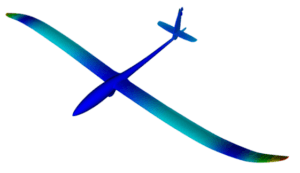
Agenda
- Overview of the Perlan II mission
- Using Simcenter 3D for building finite element models (FEMs) from CAD geometry
- Using Simcenter 3D Correlation for defining optimal measurement locations
- Using Simcenter Testlab and SCADAS for acquiring high-quality modal measurements
- Using Simcenter 3D Correlation for improving simulation predictions
- Using ZAERO for aeroelastic predictions
- Using Simcenter Testlab for flight monitoring